Sustainability Development
Download ESG Report
Innovative Products Services
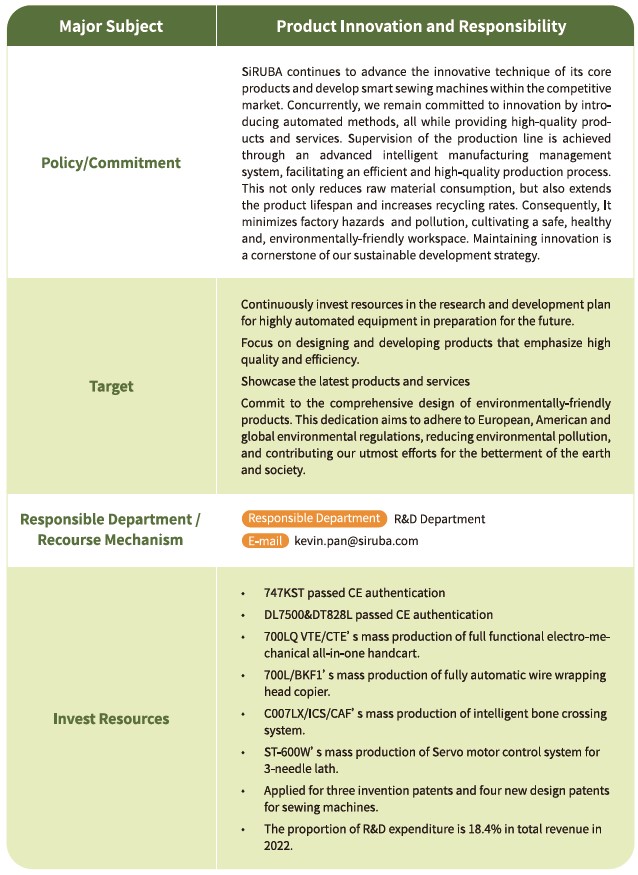
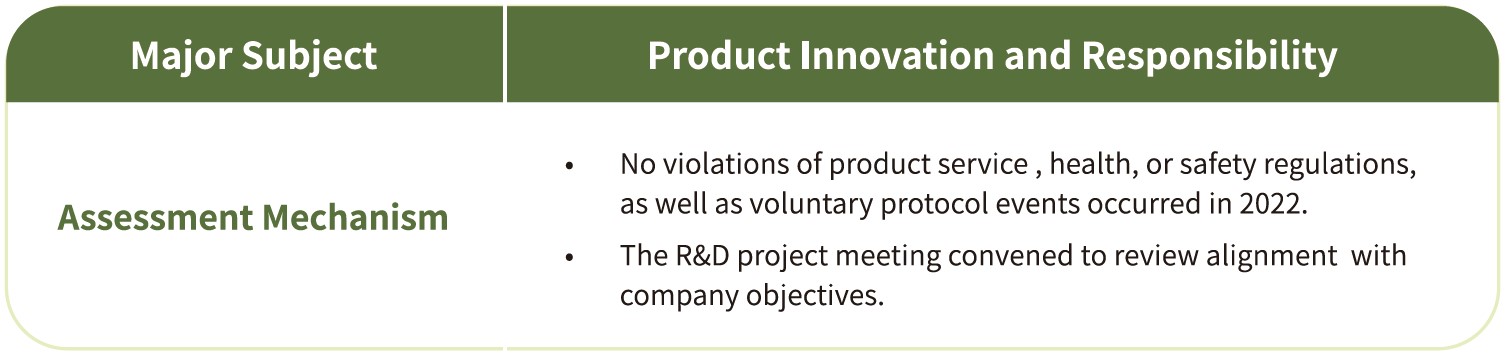
Product Liability and Security
SiRUBA s core competence lies in providing cutting-edge sewing equipment and market-positioning for global garment manufacturers. The six core values of product development are “Automatically, intelligentized, energy saving, waste reduction, emission reduction and circular economy reflecting our commitment to sustainable sewing practices. In our product development efforts, we employ servo motor direct drive and oil-free/ micro-oil structure design to enhance power efficiency in high-efficiency products. By utilizing the direct drive mechanism instead of the traditional clutch motor, we are able to reduce electricity consumption by 30%, resulting in lowered emission. SiRUBA is also continuously researching semi-automatic and fully-automatic product designs to boost garment production efficiency. Precise control of the activation timing of pneumatic elements is achieved through electric eye control, and leading to a 20% reduction in the frequency of negative pressure pneumatic element openings. Moving forward, our primary focus in product development is to prioritize reducing environmental pollution and societal impact.
Automatically and Intelligentized
SiRUBA has incorporated the assistance of information technology to develop a quality control system aimed at ensuring the products’ quality. Based on optical principles, we have implemented an Automated Optical Inspection (AOI) process to detect surface irregularities of object through computerized image processing. This process verifies the absence of abnormalities or defects. The AOI system is automated, swift, precise, and exceptionally stable, thereby replacing the conventional manual visual inspection approach. This transition significantly enhances the manufacturing process while minimizing the risk of faulty products. Utilizing the AOI principle to gauge measure the extent of oil deposition, we determine whether the machinery passes the inspection criteria and subsequently upload the data to the cloud to generate on-site display boards. The gathered information is then consolidated within a cloud-based
platform designed for monitoring oil leakage areas. Through extensive analysis of this data using big data techniques, long term trends in oil leakage can be identified. The overarching objective of this endeavor is to prevent, safeguard, and mitigate environmental pollution.
Circular Economy
To address the pressing issue of global sewing and the rapid environment pollution caused by fast fashion, SiRUBA is taking on its society responsibility as a leading supplier in the sewing industry. We have embraced the principles of the circular economy in our pursuit of new product development, centering around the pivotal goal of “zero oil zero waste.” This vision drives our efforts. This vision drives our efforts. One of our latest innovations is the oil-free sewing machine, a result of incorporating cutting-edge technology involving diamond-coated surface treatments and innovative grease lubrication designs. This groundbreaking technology can significantly reduce oil emissions from sewing machines by as much as 50%. Furthermore, SiRUBA has introduced the groundbreaking garment rag sewing trouser headphones which are designed to facilitate the recycling of textile rags. Concurrently, we have established a partnership with our cultural and creative foundation to propel the “ReSew’s Program” forward. The primary objective of this initiative is to generate recycled value through the research and development of sewing machines tailored for there-sewing waste materials. This encompasses a diverse range of materials, including textile waste fabrics, surplus stock fabrics, defective textiles, sample fabrics, and second-hand recycled fabrics.
Quality Assurance
We adhere to national environment law standards and fulfill the requirements of the IS0 9001 International Quality Management System to meet the customer demands, maintain standards ,and enhance brand value. We have established a multitude of quality standards, which include the “Incoming inspection standard,” “Process inspection standard, “ Finished product inspection standard,” and “Quality appraisal standard.” Our approach involves continuous improvement through the PDCA (Plan-Do-Check-Act) cycle to effectively address risks. To ensure the delivery of the highest quality products and services to customers, we have implemented a rigorous audit management system. Meanwhile, SiRUBA offers a diverse range of machine types, and the integration process is intricate necessitating
collaboration with external vendors for development. During trial installation, if issues arise, we engage in through communication with vendors via methods such as video conferencing or physical exchanges. This iterative communication helps pinpoint problem areas, facilitating meticulous testing and modification by our R&D engineers. This approach leads to smooth solution in product development. Year after year, we maintain a commitment to innovation, consistently meeting customer expectations by delivering products that align with their needs.
Development of oil-free sewing machine-Ultra high-speed Interlock Machines C007L/LX Serial
SiRUBA’s Ultra high-speed Interlock Machines CD07LJLX Series features a design specifically engineered to prevent lubricant leaks and the infiltration of dust into the needle bars and hooks of the sewing machine. This design not only safeguards against these issues but also regulates the oil leakage for optimal lubrication conditions,promoting extended service life while maintaining consistent operation.
The CO07L/LX series incorporates a novel oil seal structure that enhances the isolation of lubricants, isolation performance, effectively mitigating instances of lubricant flinging. To further enhance performance, we employ high wear-resistant FKM (Fluoroelastomer) material. FKM, known for its resistance to high temperature,oil,solvents and chemicals, is a critical synthetic rubber in industries such as aerospace, automotive, petrochemicals, and industrial pollution control. When applied sewing machine oil seals, it significantly enhances sewing machines performance.
We have pioneered the latest oil resistant technology by combing components of the CD07LX with upgraded materials. For instance, the needle bar surface is treated using a special diamond-like carbon method, ensuring oil-free operation during sewing. This new surface treatment technology integrated with a grease lubrication design, reduces oil splatter by 50%, all the while simplifying the post-cleaning process in the garment manufacturing process. This results in a significant reduction in water usage and cleaning complexity during the manufacturing process.
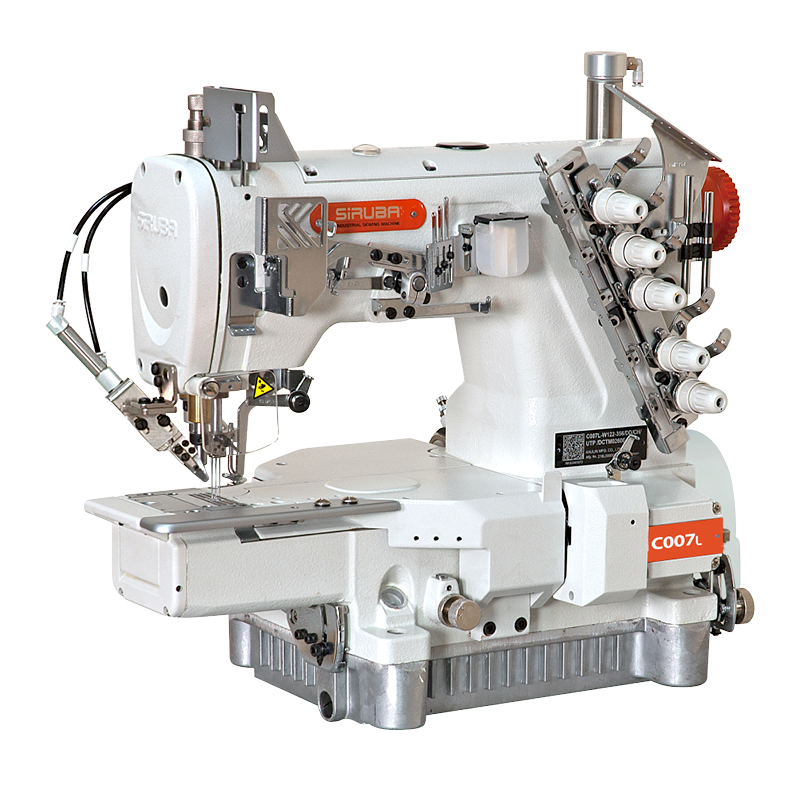

Reducing Waste Fabric and Shredding Recycling
In garment factories, a significant amount of irregular fabric scraps is generated during the cutting process, often referred to as “offcuts” or “tailing” While some of these scraps are repurposed into items like rags, oil wipes, or even turned into mops, a majority of them are unfortunately discarded as waste, often being burned or buried. This practice contributes to air pollution and wastage of water resources. Through the promotion of various research and development initiatives and activities, SiRUBA endeavors to propagate the concept of “sustainable fashion” to a wider audience.
To address this issue, SiRUBA has developed the FOO7K/FBQ model of garment rag seamless trousers with integrated earphones. This innovative design allows for the recycling of irregular fabric scraps produced during the cutting process. These scraps are sewn into trousers, offering a practical solution for garment factories to recycle and repurpose their offcuts, contributing to the reduction of waste in the fashion industry.
Reduced Seam Usage
Inserging machines lacking a thread cutting device, user traditionally kept the motor running after sewing to produce a length of 10 to 15 centimeters of sewing thread, which was then cut using the sewing machine. This practice often led to unnecessary thread wastage. T counter this issue, SiRUBA has developed a novel type of serging machine cutting device,the ECA/ECB model. This innovative cutting device utilizes an electric eye a to detect the fabric’s end position. It precisely controls the cutter to trim the thread at the conclusion of the sewing process while simultaneously halting the servo motor As a result, thread consumption during the sewing process is significantly reduces to a mere 3 to 4 centimeters. This advancement effectively minimizes thread wastage, enhancing the efficiency of the sewing process.
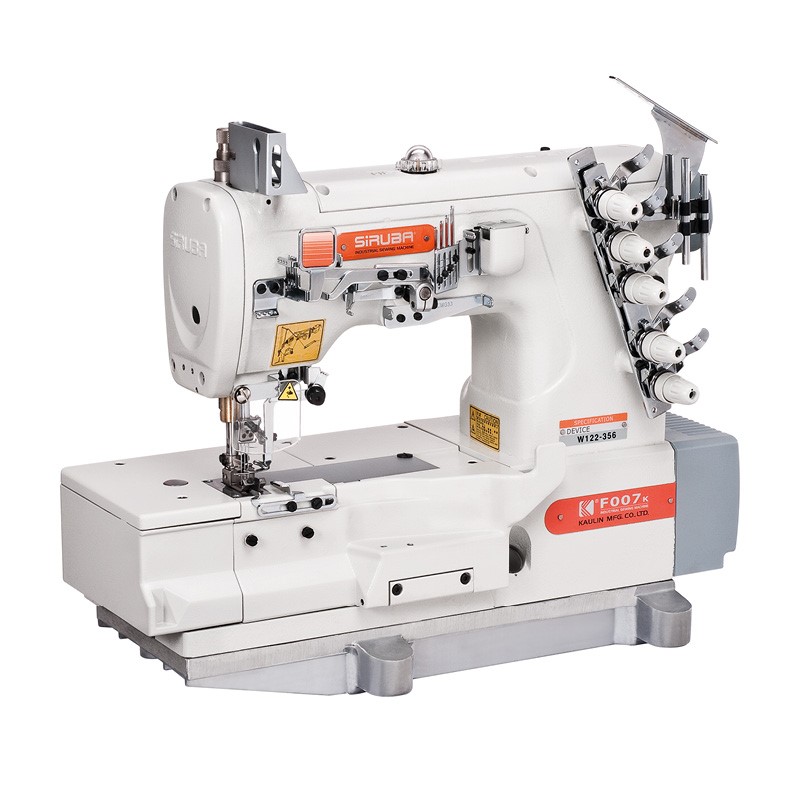
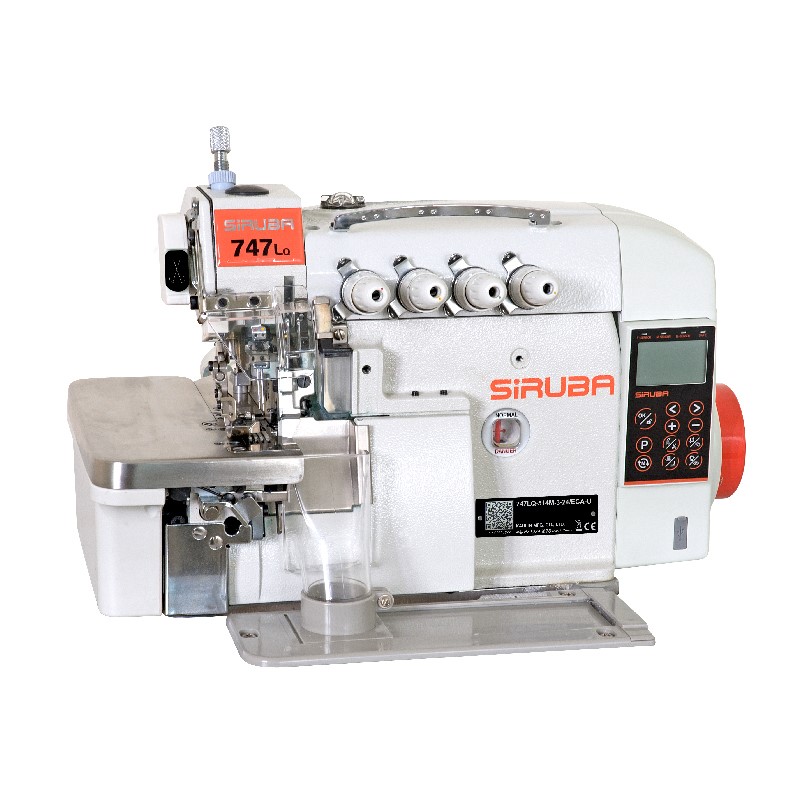
SiRUBA values every clients opinions and strives to fulfill their requests while dedicating itself to delivering top-notch service. In pursuit of this commitment, we have established a highly capable service team. This team spans across various stages, including development, production, marketing, sales, and after sales support. Each phase of our process is equipped with dedicated points of contact, ensuring swift and responsive reactions to customer requirements and expectations.
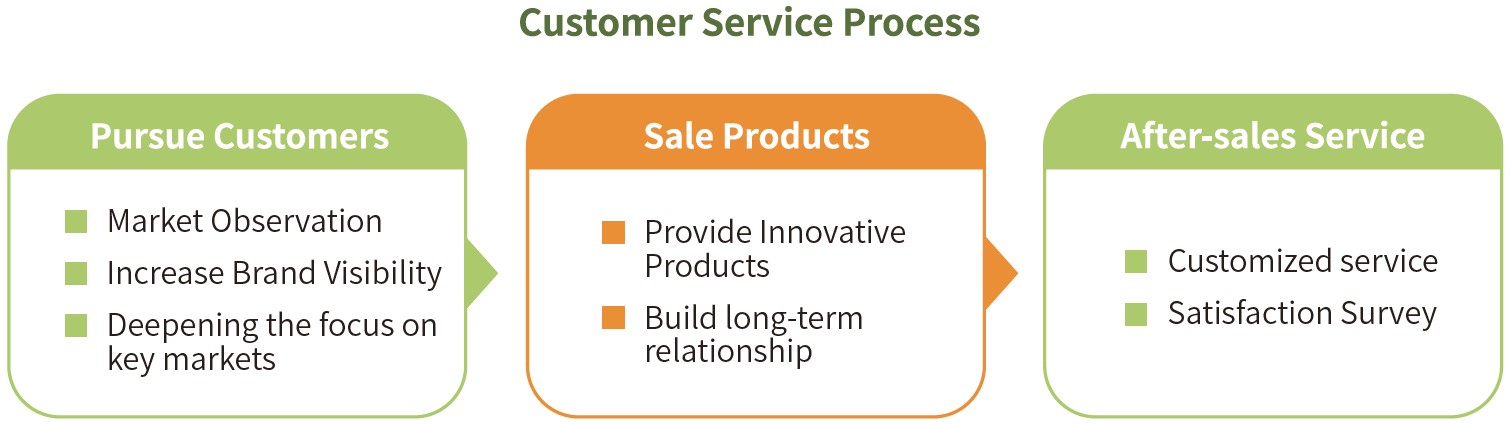
SiRUBA regards customer feedback and opinions as a fundamental cornerstone for cultivating strong customer relationships, enabling us to comprehend clients needs through multiple communication channels. Clients have the opportunity to provide insights on quality discrepancies, performance issues and future requirement via these channels. For each piece of customer feedback, SiRUBA conducts regular examinations and analyses, formulating appropriate improvement plans and establishing comprehensive response protocols. Annually, our business unit conducts a customer satisfaction survey, directing all inquiries to the respective departments for responses and enhancements. Customers can also report product irregularities through the “Customer Service Process” BPM system. Our QA unit promptly investigates these irregularities and implements corrective measures. In cases of customer complaints, regardless of the severity, SiRUBA dispatches personnel to rectify the situation. We actively revise design flaws and reaffirm our commitment to customers and quality. Notably, there were no customer complaints related to product safety or environmental regulations in 2022.
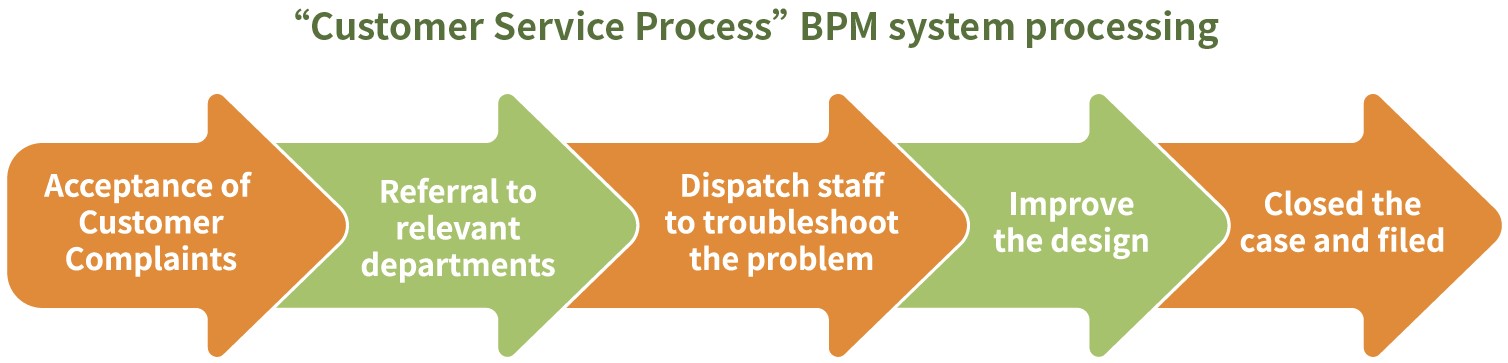
Digital Customer Service
The rapid changes brought about by Covid-19 have significantly impacted marketing and sales strategies. In response to the escalating demand for digital services from both customers and users, SiRUBA has embraced innovation, offering cutting-edge digital services and enhanced e-commerce ordering experiences to cater to the impending “digital era”.
- The establishment of a customer self-service platform (ICT Platform) designed to promptly provide clients with the information they require. This platform also features an online purchasing system that expedites the ordering process. Beyond just streamlining issue
resolution, this system reduces customer time and effort, spent by customers, thereby bolstering the overall customer experience. - SiRUBA has introduced the industry’s pioneering use of QR Code for scanning products, providing the comprehensive product details. Moreover, this technology ensures customer rights, as the technical service department can instantly access in spection Values using the QR code. This approach minimizes customer losses stemming from troubleshooting delays, while also safeguarding the company’s reputation and customer relationships.
- The establishment of an E-commerce system simplifies B2B trading procedure for users. This system streamlines the entire process, from product selection and order placement to shipment tracking, enabling customers to efficiently engage in fast and accurate merchandise trading collaborations.
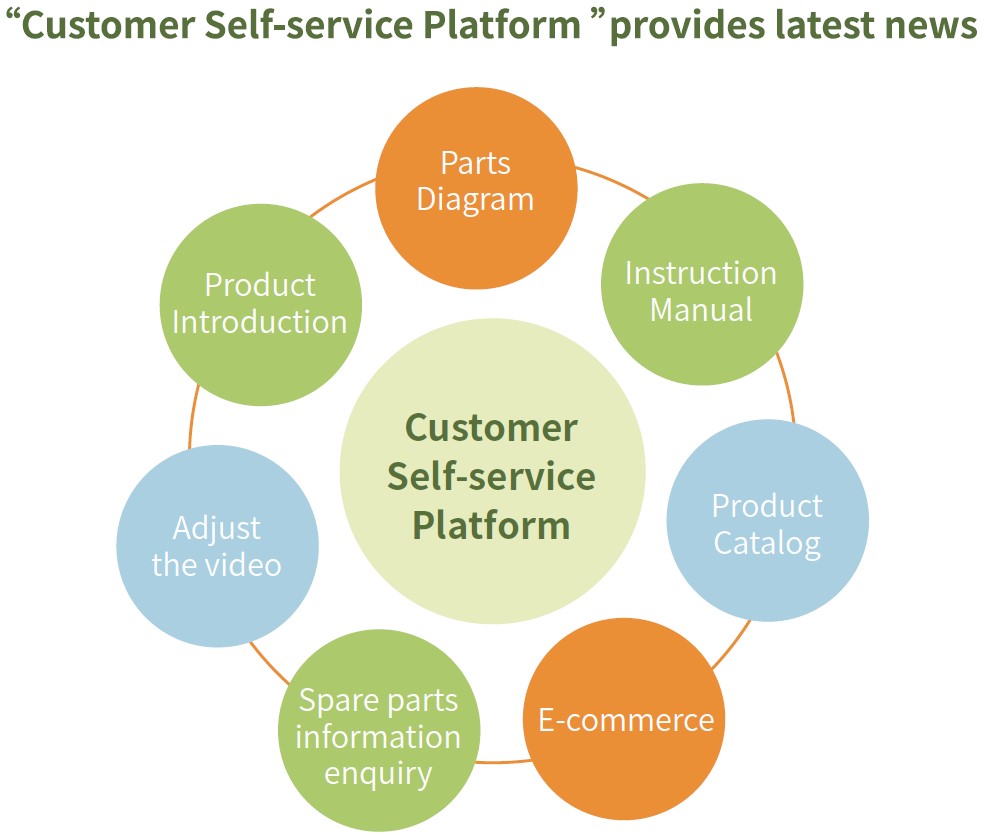
Diversified Product Marketing
While SiRUBA remains rooted in traditional industries, we have actively embraced social media and modern marketing tools in recent years. Our aim is to enhance brand visibility and extend our market reach through diverse marketing approaches, all while fostering strong cooperation relationship.
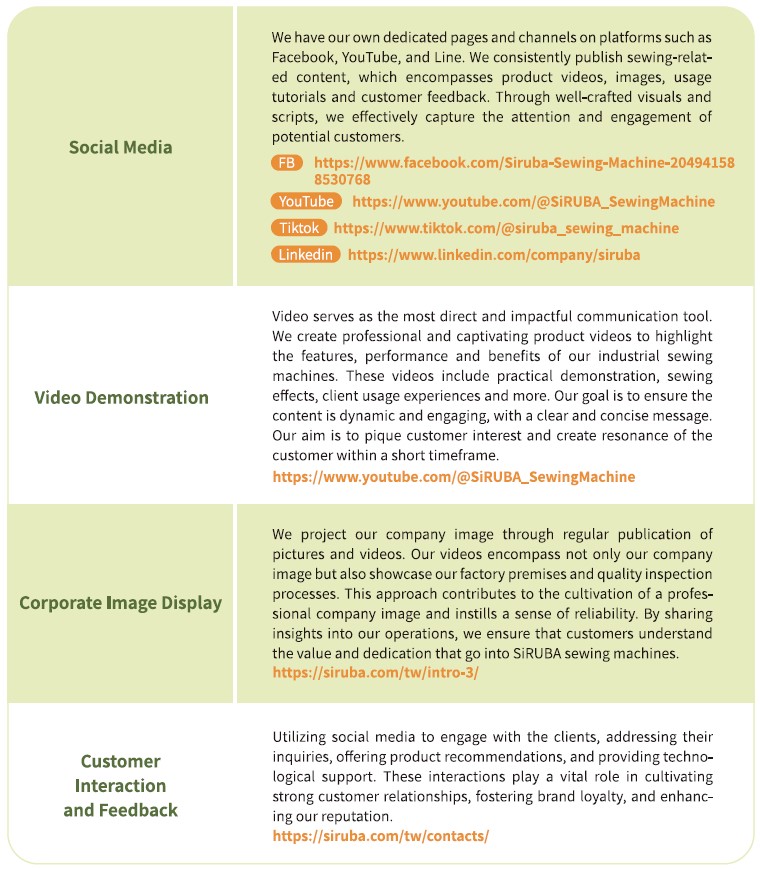
Customers Privacy Protection
We recognize the significance of safeguarding classified information for maintaining a competitive edge. The company has implemented a personal information protection management system that outlines the necessary rules and regulations for effectively overseeing business secrets and confidential information not yet made public. This systematic approach ensures the protection of both customer and vendor interests. Notably,there were no complaints regarding customer privacy breaches or confidential information leaks in 2022.